Metenova tools
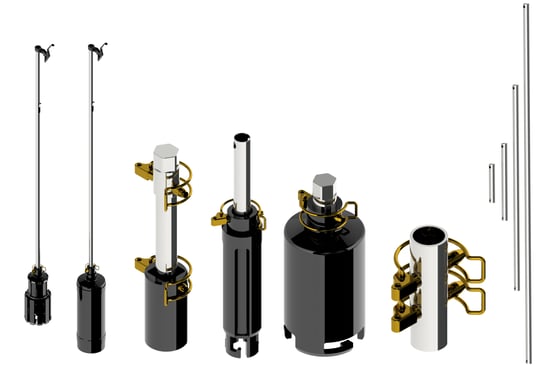
Lifting & tightening
The Lifting Tools are used for assembly and disassembly of Mix Heads. Tightening Tools are used for assembly of Male Post and the High Shear Stator. These tools make installation and disassembly of our Mixers both easy and safe. It is possible to build together several extensions to adapt the tools to reach down into deep vessels.
Download datasheet
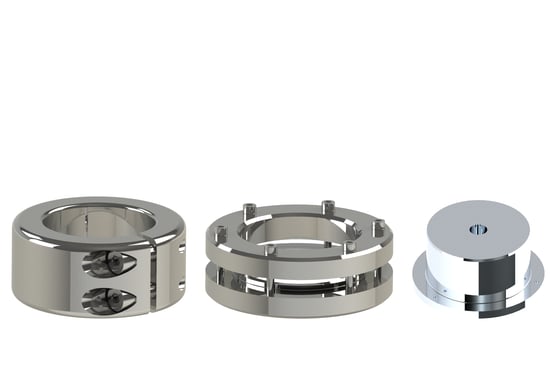
Welding
Our selection of welding tools is the ideal helping hand when welding tank plates into the vessel. Making sure you get the ultimate conditions for your mixing.
Download datasheet